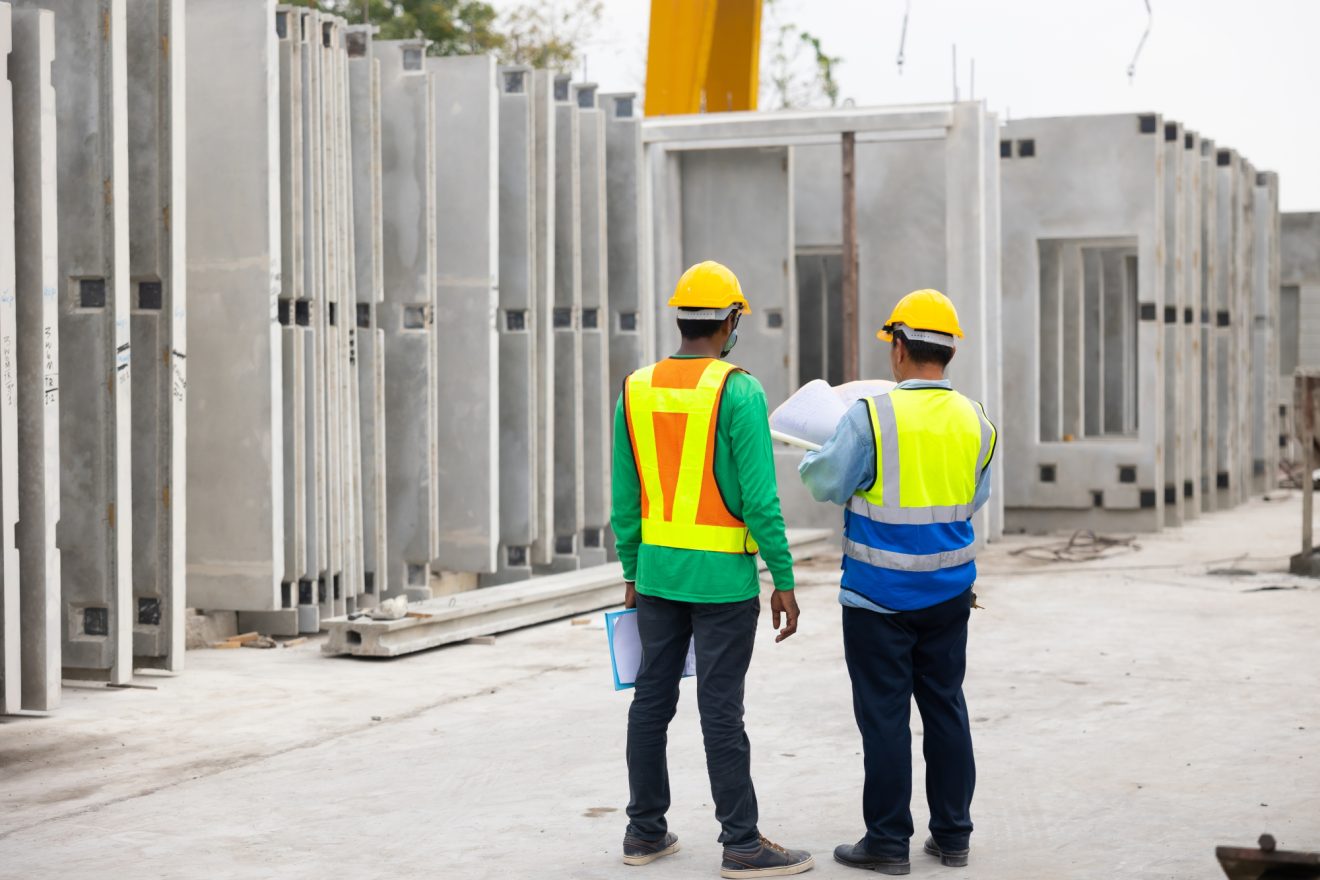
Think of the thousands of pieces involved in a commercial real estate construction project. What if you could cut that number in half?
In recent years, builders of all sizes have partnered with off-site manufacturers to incorporate prefabricated components to cut down on a build's complexity and speed up the process. Using prefabricated products can help you increase output, which ultimately helps your bottom line. Imagine being so efficient you could build 12 high-quality houses in the time it would normally take to build six.
But to be successful, you’ll need additional organization and planning. It’s a good idea to bring in manufacturers who prefabricate building products from the start of the construction process. Your build schedule should also align with the factory’s timeline. And remember, having prefab software that integrates everything is just as important as the building components.
Let's walk through a quick primer on prefabrication, how it helps builders, and tips for getting the most bang for your business.
Prefabrication Basics
Prefabricated building materials have been around for decades. You’ve likely seen or used roof trusses or other pre-built construction components on a project. The term “prefabricated” or “prefab” refers to creating building components in a manufacturing facility. The components are then assembled at the building site.
Manufacturers typically use one of three prefab methods. Panelized construction uses flat, 2D structural components to create building frameworks. Modular construction creates 3D sections or modules of a home that are around 70% complete and then connects them on-site. Lastly, volumetric construction uses large, pre-built modules that are almost completely finished and can be stacked and connected on-site. (Imagine putting together Lego bricks.)
Common manufactured components include roof and floor trusses, wall panels, staircases, and railings. According to the National Association of Home Builders, over 70% of builders and remodelers use roof trusses, and over 50% use floor trusses. Some manufacturers even make entirely finished kitchen or bathroom pods.
How Prefabrication Helps Builders
Saves Time
According to the Modular Home Builders Association, simultaneously developing your site while a manufacturing plant constructs the home can reduce your build schedule by 30% to 50%. Take framing, one of the most time-consuming parts of a build. Now imagine a jobsite with pre-built wall panels that already include electric and plumbing chases. How much time would you save on-site?
Reduces Costs
Using prefab elements can help save money by cutting down on how much time you need workers on-site. Traditional construction often means bringing in a big crew, which gets expensive with all the skilled labor, overtime, and project management. But with off-site modular construction, you could save up to 20% compared to conventional construction.
Improves Quality Control
Since prefabricated materials are made in a controlled setting, you get precise products and better quality control — which could also save you headaches with warranty issues down the road. As a bonus, factory production produces less waste, which means there’s less of it to handle at the jobsite.
Allows Multitasking
While you’re busy excavating and laying the foundation, your prefab components are built at the same time, so essentially you’re multitasking. Those products will be ready when you are, and you won’t have to worry about them stacked outside too soon, exposed to the whims of water and wind.
Projects That Work Best With Prefabricated Components
Many builders use prefabricated products for single-family and multifamily residential, commercial, and industrial projects. They’re choosing prefab components for onsie-twosies, infill projects, custom homes, or large developments.
For a hotel or multifamily apartment project, it’s a no-brainer to stack bathroom pods one atop another. Imagine the first-cost savings (related to labor and design). Or, if you work on an island, where it’s difficult to get labor and supplies, barging in volumetric modules may save you boatloads of money. Doing a city infill project? Prefab components or stacking full volumetric modules means fewer trucks and deliveries, fewer disruptions to the neighborhood, and less waste. Say you need to do routine maintenance or make upgrades on a commercial site like a transit station. Using prefab elements can minimize disruption and the amount of time you’ll need to be on-site.
Finding Success With Prefabrication
A building project can go off the rails in many ways. Making preconstruction a top priority can help keep you on schedule and on budget — particularly if you choose prefabricated components. If you do, you can take a few steps to set yourself up for success.
Meet early and often with your product suppliers, and match your schedules with theirs for a seamless process. Work out the “what if?” scenarios on design changes, material shortages, or site issues sooner rather than later.
Have a plan for transportation and logistics. Some prefab manufacturers have this part taken care of; with others, transport might be your responsibility. But you're a builder and not a logistics expert. Will the components fit on a trailer? Will the trailer be able to maneuver narrow roads and low bridges and still get to your site? If you're doing a housing development, do you have a large tent to cover a component staging area? If you're doing a city infill or multifamily project, is there room to maneuver on crowded streets?
Streamlining Your Next Build
The right software can help you streamline the logistics for a smooth delivery and build. It can also help coordinate every aspect of the project, from architectural design, scheduling, and implementing milestones, all the way through production handoff and construction.
Overall, using prefabricated components can lead to major labor savings because of the simplicity of on-site assembly. You’ll gain efficiency by front-loading production and quality assurance. And ultimately, since everything is made in a factory with precise measurements and controls, you’re likely to end up with more accurate results.